Installation and debugging of Refrigeration equipment in Cold Storage
- Share
- From
- First Cold Chain
- publisher
- SUNNY
- Issue Time
- Apr 1,2022
Summary
Installation and debugging of Refrigeration equipment in Cold Storage
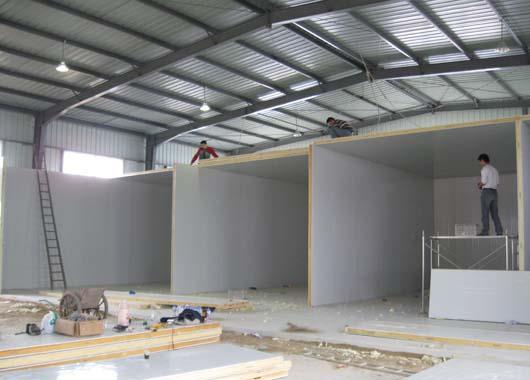
- How to install the Cold Storage
- A.Assembly and installation of Refrigeration unit
- If the evaporating temperature is below-15 degrees, the gas-liquid separator shall be installed and the appropriate amount of refrigerating oil shall be added to the gas-liquid separator and the appropriate amount of refrigerating oil.
- 2. Compressorbase should be installed with rubber seat.
- 3. Theinstallation of the unit should have maintenance space, easy to observe the instrument and valve adjustment.
- 4.Thehigh-pressure meter should be installed in the liquid storage irrigation valve three-way place.
- 5.The overall layout of the unit is reasonable, the color is the same, each type of unit installation structure should be consistent.
- B.Cold room and installation of chiller
- 1. When the position of hanging point is selected, the best position of air circulation is considered first, and then the direction of reservoir structure is considered.
- 2.Thegap between chiller and storage plate should be greater than the thickness of chiller.
- 3.Allchiller plugs shall be fastened and sealed with sealant to prevent cold bridges and air leaks.
- 4.When the ceiling fan is overweight, the beam shall be made by using angle 4 or angle
- 5, and the beam shall be straddled to another roof and wall board to lighten the load-bearing.
- C. Installation Technology of refrieration Pipeline
- 1. The diameter of copper pipe should be chosen strictly according to the suction and exhaust valve interface of compressor. When the condenser and compressor are separated more than 3 meters, the pipe diameter should be increased.
- 2,Condenser suction surface and wall keep above 400mm distance, outlet and obstacle keep more than 3 meters distance.
- 3,The inlet and outlet diameters of liquid storage tanks shall be based on the exhaust and outlet diameters indicated on the sample of the unit.
- 4,Compressor suction lines and chiller return lines shall not be less than the size indicated in the sample to reduce the internal resistance of the evaporating line.
- 5. When the position of the condenser is higher than that of the compressor, the exhaust pipe shall have a certain slope. When the position of the condenser is higher than that of the compressor, the exhaust pipe shall be sloped to the condenser and a liquid ring shall be installed at the exhaust port of the compressor to prevent the cooling and liquefaction of the gas from returning to the high pressure outlet after shutdown. When rebooting, the fluid is compressed.
- 6.The U-bend should be installed at the outlet of the return pipe of the chiller, and the return pipe should be sloped to the direction of the compressor to ensure the smooth return of oil.
- 7. The expansion valve shall be installed as close as possible to the chiller, the solenoid valve shall be installed horizontally, the valve body shall be vertical and the direction of discharge shall be noted.
- 8. If necessary, install a filter on the compressor return line to prevent the system from entering the compressor and remove moisture from the system.
- 9,Allsodium and locks in the refrigeration system should be lubricated with refrigerated oil before fastening, and the sealing property should be strengthened. After fastening, wipe clean, and the root of each door-cutting disc should be locked.
- 10,The expansion valve temperature package is fastened at the evaporator outlet 100mm-200mm with metal clamp, and wrapped with double layer heat preservation.
- 11,After the welding of the whole system, the air tightness test should be carried out, the high-pressure end filled with nitrogen 1.8 MP. Low pressure end filled with 1.2MP nitrogen, during the filling period with soap water for leak detection, carefully check the welding joints, flanges and valves, after the leak detection is completed to maintain pressure for 24 hours without falling off the pressure.
- D. Installation Technology of Electronic Control system
- 1,Each pin marks the wire number for overhauling.
- 2,Strictly according to the drawing requirements to make the electronic control box, and connected to do no-load experiment.
- 3,Name each contactor.
- 4,The wires of each electrical component are fixed with binding wire.
- 5,Electrical contact pressing wire joint, motor main line connector, application wire clamping.
- 6,Each equipment connection must lay the wire pipe, and fastens with the clip, the PVC cable pipe is connected by the adhesive, the pipe orifice is sealed with the rubber cloth.
- 7,The distribution box installed horizontal vertical, environmental lighting is good, drying in the house is easy to observe and operate.
- 8,Wire on-line pipe area must not exceed 50%.
- 9,Wire selection should have a safety factor, unit operation or defrosting when the external temperature of the wire should not exceed 4 degrees.
- 10,Wires should not be exposed to the open air, in order to avoid long-term sunburn wind blowing wire skin aging, short circuit leakage and other phenomena