How to decontaminate cold storage refrigeration system after installation?
- Share
- From
- First Cold Chain
- publisher
- Sunny
- Issue Time
- Apr 1,2022
Summary
The reason for blowing pollution after installation of the refrigeration system is: in the process of installation or maintenance of the refrigeration system
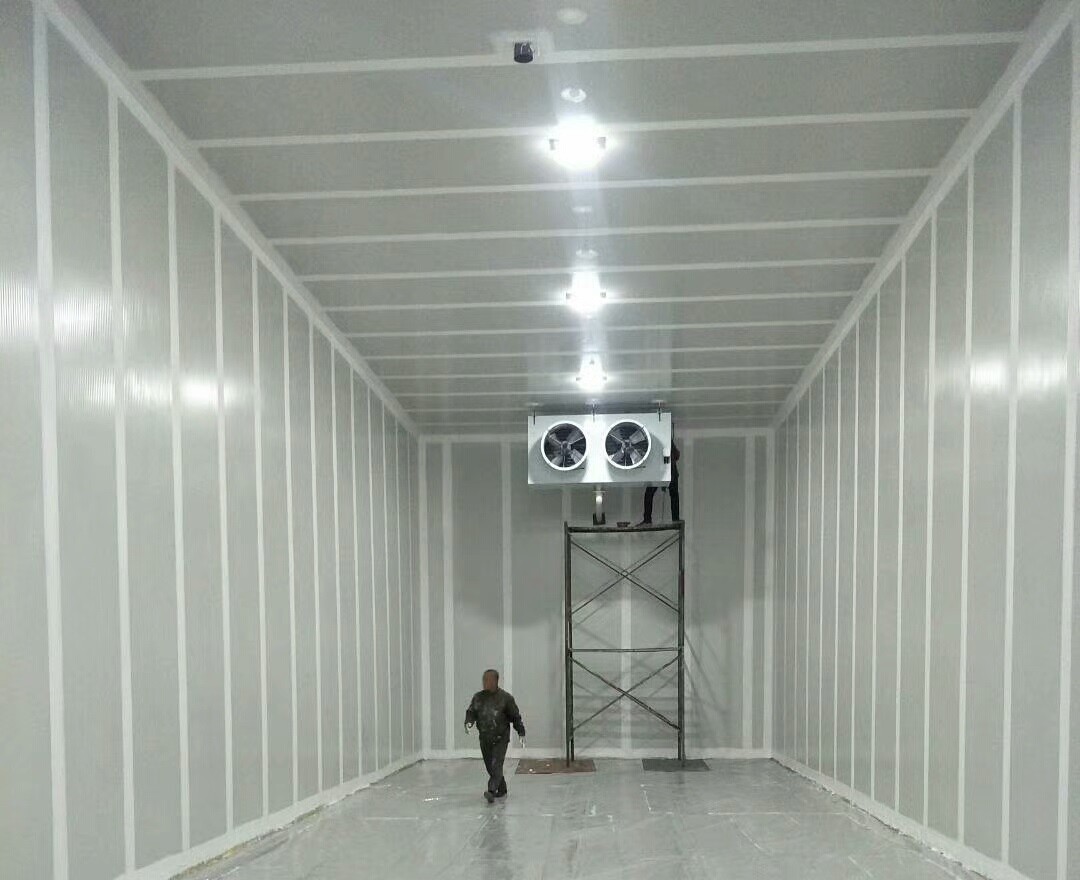
How to decontaminate cold storage refrigeration system after installation?
The method of blowing pollution after installation of refrigeration system is as follows: blowing pollution of refrigeration system by sections. The procedure is to blow the dirt of the high pressure part of the refrigeration system, then the dirt of the low pressure part of the refrigeration system.
1. It is to connect the spare orifice of the compressor high pressure cut-off valve and the nitrogen cylinder with a pressure-resistant pipe, remove the drying filter from the system, open the nitrogen cylinder valve, and blow the high-pressure section of the system with 0.6MPa pressure. After charging to the 0.6 MPa gauge, stop inflating. The cork was then pulled out quickly and the system was discharged with high-speed airflow. And put a piece of white paper at the outlet to detect dirt. Depending on how clean it is, if the white paper is cleaner, you can stop blowing if there is no dirt washed out of the gas.
2.It is to connect the spare orifice of the compressor low-pressure cut-off valve and the nitrogen cylinder with pressure-resistant pipe and still use the 1000 dryness filter interface as the detection port, open the nitrogen cylinder valve, and use 0.6MPa to gauge the low pressure segment of the nitrogen blowing system. White paper is still used in the air outlet to detect the contamination, and after confirming the contamination, the cooling system of the small-scale cold storage at the end of the blowing process should carry on the pressure test leakage work after completing the blowing of the system. The method is to install a 0~2.5MPa pressure gauge on the backup orifice of the compressor high pressure stop valve and a 0.1~1.6MPa pressure gauge on the multi-purpose orifice of the compressor low pressure stop valve.
.